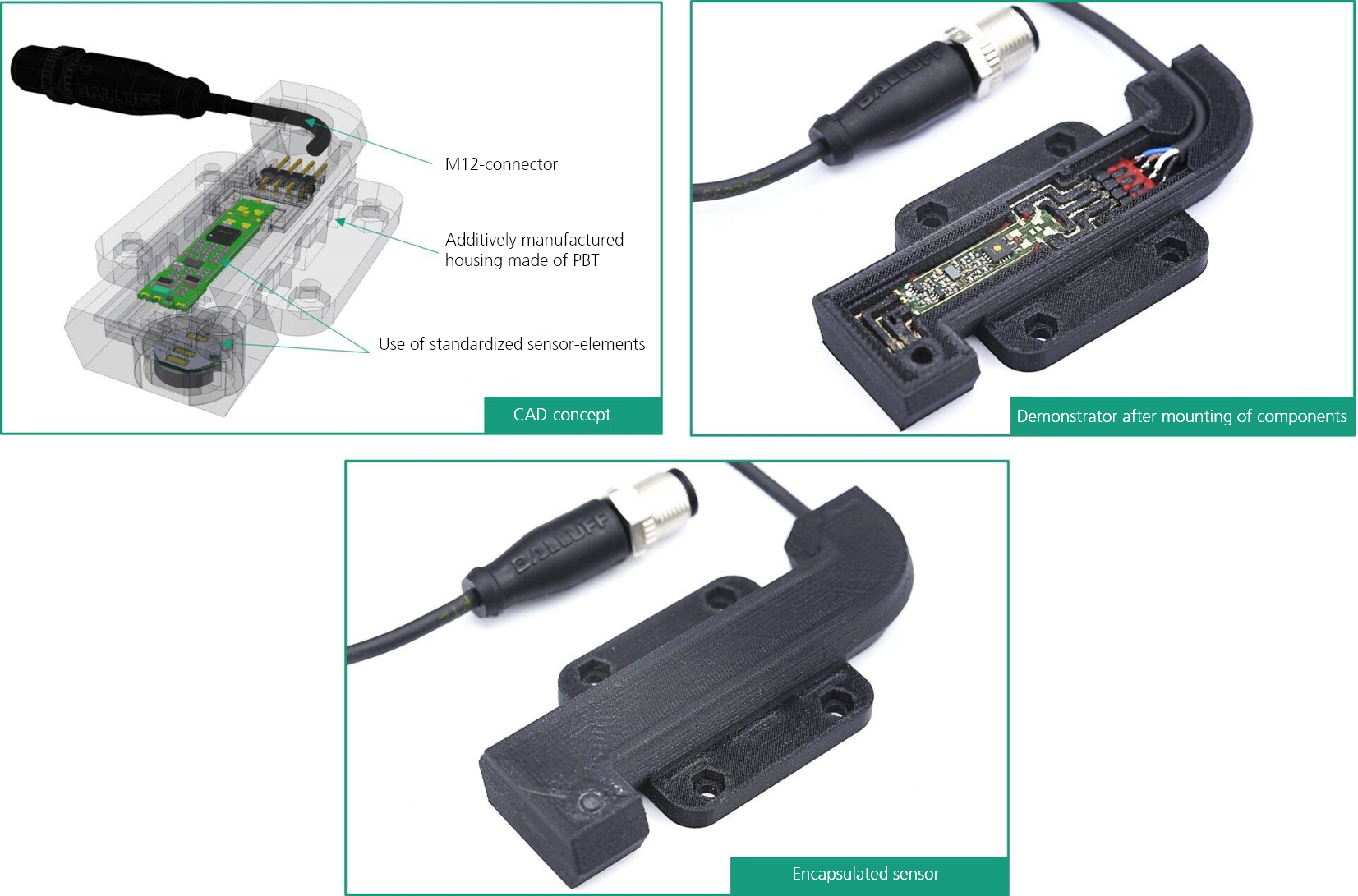
The research project "Additive manufacturing of individualised sensors" focused on solving the challenges of directly integrating electronic components into additively manufactured plastic packages with individual shapes. The overall objective of the research project was to demonstrate the additive manufacturing of individual sensors using the Arburg Kunststoff-Freiformen (AKF) in compliance with industrial standards and norms. Using the example of a standard inductive sensor, the project team tackled this challenge.
Inductive sensors in customised design are interesting for tasks in automation technology, since this allows for optimal adaptation to the application. Currently used inductive sensors are constructed in an elongated metal housing in which a coil, a circuit board and a plug are installed in a fixed constellation - a standard component with the same shape every time. It is often used because it recognises when an object is approached on the basis of the electromagnetic field. However, inductive sensors have so far been useless if their shape has to fit into a certain environment, such as a robot arm or a gripper finger. So why not print the sensor housing from plastics so that it can be manufactured in any shape and then integrate the low-cost individual components of the sensor from series production into the housing in the desired spatial orientation during printing?
This question was addressed in the research project "Additive manufacturing of individualised sensors" by a research team from Fraunhofer Institute for Manufacturing Engineering and Automation IPA. It was supported by employees of the system manufacturer for plastics processing ARBURG GmbH & Co. KG and the sensor and automation specialist Balluff GmbH. During the one and a half year project, the experts developed a hybrid process chain consisting of additive manufacturing of the plastic housing using AKF, the insertion of the electronic sensor components and the production of the electrically conductive connection between the individual functional components by precisely dispensing a conductive silver paste.
Using the hybrid process chain, individualised inductive sensors were manufactured on the basis of an exemplary demonstrator design and their functionality was subsequently tested in industrial qualification tests at Balluff's test campus. The individualised sensors had to withstand temperature changes and vibrations, they had to be waterproof and pass an electrical insulation test. By optimising the design and manufacturing process, the tests were successfully completed.
The picture shows the demonstrator of the customised sensor in the different production stages: CAD concept (top left), after integration of the electronic components (top right) and as a finished demonstrator (bottom).
Publication:
Manufacturing of individualized sensors: Integration of conductive elements in additively manufactured PBT parts and qualification of functional sensors (https://doi.org/10.1007/s40964-023-00449-0)
Link:
https://interaktiv.ipa.fraunhofer.de/mass-personalization/sensoren-aus-dem-drucker/
Project:
Additive manufacturing of individualised sensors
Contact:
Fraunhofer IPA, Dipl.-Ing. Patrick Springer, patrick.springer@ipa.fraunhofer.de, +49 711 970-1996